A week of encountering many problems again, and finding solutions for most of them... Meaning in some cases re-designing part of my new wing design again, and changing back to some part of the old design.
While I was working on the first joint for the 'hand' of the wing I realized another couple of mistakes I had made. I had designed the attachment for the ball joint plate + pivoting feathers both at the front (see scale drawing some posts back) with the idea that it would allow the joint to be a bit thinner as a whole. However, at the same time it would get in the way when turning for the folding of the wing. Another mistake was that I had made the lower part for the pivoting feathers sticking out at the side. It made sense when I designed it first, but now I noticed it would really affect how much the joints could be turned. I re-designed it making it square again, but slightly longer at the ball joint side, slightly shorter at the pivoting joint side.
I tried to find a way to solve the problem of the clamp part being in the way at the front, and after thinking of two complex solutions decided that it would be fine to have that part at the back. This would make the whole joint a bit thicker as it would have things sticking out at two sides, but solving a lot of problems too, so worth that sacrifice.
Changing the joints, early design in progress at top,
finished joints with changes below.
Silver soldering still is something I need more practice in clearly. I had plenty of opportunities this week, and still been getting it wrong plenty of times. Expensive practice... but hopefully I'll get better at it soon. Also a time consuming practice, as every time getting it wrong means cooling down, cleaning up and setting up the parts again in the right position with flux and solder, etc. and if it goes wrong again doing all that again, and again, and...
Then I found another major mistake in the design. I had already made the ball and socket joint between the upper and lower arm (elbow) and soldered it all together, then went testing its movements. I had deliberately changed this joint as I thought the hinge joint was too limited in its movement. I was really puzzled about this for a while, even wondering if birds maybe had some different type of more flexible joint here. A silly thought really, but I thought at least it 'wouldn't harm' having some more moving possibilities. I thought the turning around of the elbow would make things easier, as it looks when turning around your arm as if something in your elbow is moving too. Duh! It's the skin that is moving of course, not the bones... What I thought would give more flexibility was actually limiting the joint more now, as the ball and socket joint would not allow to be folded entirely. I was still believing that I could adapt it a bit for a while, but actually messed it up only more in that way. I was trying to file parts away to allow more movement, but I soon realized that it was just not going to work. I remembered now that I had not been able to fully judge the movement of the old wing design as there was no shoulder attached then. Even though I knew this then, it must have been because of this that I got confused and made the mistake. Now it meant I had to remake this part and make it into a hinge joint again.
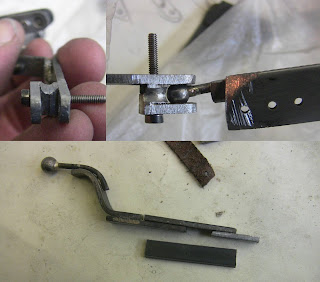
Trying to 'fix' the ball joint mistake, then changing it to a hinge joint.
The next day I continued working on the hinge joint and also re-made the upper arm plate. I had to re-melt the silver solder to use some parts again, and get them soldered to the new parts again. This day brought a lot of frustrations as the soldering kept going wrong. I could find no other way to get everything soldered then using a lot of clay near to the part I was soldering, even directly underneath it. This meant a lot of exploding clay and bits of dried clay flying onto the surface I was trying to solder. I almost lost hope when somewhere in the middle of a complete mess of clay, flux and black surface suddenly it had worked, against all my expectations. Not much later it actually seemed like the wing was coming together!
Top to bottom: setting up for soldering (one of many attempts),
The finally finished and roughly cleaned up part,
upper and lower together.
I was carefully checking all the movement of the wing this time before moving on, but this time all seemed to work fine... I continued making all the feather rods. The next thing is to find a good solution for the fanning mechanism, but other then that the wing is complete.
Testing the folding movement with the parts finished so far.
The finished wing, folded.
The finished wing, spread out.
Now, there is not much time to celebrate the success as there is not much time left before the break to get more of the body parts done so I wanted to get most out of the time I still had.
I had most parts for the middle part of the body ready to be soldered together, so I hoped to have a bit more success with soldering this time and get more done. Of course it took long again. I had noticed that the joint plates of the joint connecting the two wings was already slightly bent, or at least it looked like that. I thought it would be a good idea anyway to avoid this getting worse and make this part as strong as possible as it would be an important central part of the puppet, having to carry a lot of weight from all the connected limbs. So I decided to 'fill up' some of the gaps with metal plates, which of course was easier said then done. I had a lot of problems this time trying to solder the plates together, as I needed to clamp them together with the screw while soldering, but at the same time didn't want them to be soldered entirely together. I would still have to be able to open the joint. This meant that I had to be really careful about where the solder could flow. In most cases though the solder stayed too much at the solder and the bond wasn't strong enough. I tried soldering both side, but keeping the opening at the same place... It was really fiddly, and while trying to solder one of the hip joints the solder did indeed suddenly flow too far. I wasn't even able to loosen the screw, and then I 'screwed up' it's allen key hole by trying, so there is no way anymore now the get it out. I could try it by re-melting everything. But for now I gave up and concentrated on getting at least the chest part finished as far as possible and solder two ball bearings on the connecting part for the chest and hip part. I had it just about done except some filing and re-drilling still has to be done to have the ball bearing from the wing shoulder attachment fit in, but I can do that later at home.
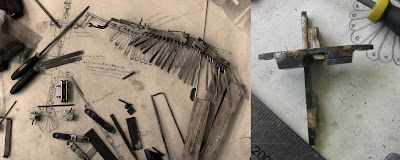
Friday work, messing about with the chest part for a long time, finally soldered at right.